Drivers Diode
Diodes' offline LED drivers provide a simple cost-effective solution for offline lamps, which includes retrofit lamps as well as T5/T8/T10/T12 replacements and dimmable LED bulbs. Diodes' medium voltage DC-DC high brightness LED drivers combine a small footprint and high power density with operating voltage up to 60V. Pin Diode Drivers APITech offers a complete line-up of PIN Diode Switch Drivers with output current capability of 10 mA to 50 mA and switching speeds as fast as 6 ns. Thin film metalization on ceramic substrates ensures low parasitic capacitance for fast switching, small size, and excellent reliability.
68 suppliers for laser diode drivers
are found in the RP Photonics Buyer's Guide. Among them:
Find more supplier details at the end of this encyclopedia article, or go to our
You are not yet listed? Get your entry!
Laser diodes drivers are electronic devices which are used to supply one or several laser diodes with the required electrical drive current.Most of them obtain electrical power from the public grid, but there are also battery-operated devices.
Basic Functionality
In many cases, a diode driver simply needs to supply a constant operation current, resulting in continuous-wave operation of the laser with approximately constant optical output power.Due to the highly nonlinear voltage–current characteristics of laser diodes with a low differentialimpedance (high dI/dV) (see Figure 1), which also significantly depend on the junction temperature, it is usually not sufficient to apply a certain constant voltage; instead, the electrical current needs to be stabilized by automatically adjusting the applied voltage.This constant current mode is the function of a so-called current source.For increasing device temperature, the curve in Figure 1 is shifted to the right; one then requires a lower voltage for the same current.If one would instead keep the voltage constant, the current could rise substantially, which would further increase the junction temperature.This might even result in a run-away situation, where the laser diode is destroyed, if the current is not limited.
Note that the drive current and not the voltage determines the rate with which electrical carriers are injected into the junction of the laser diode.Therefore, the optical output power is strongly linked to the drive current and less directly to the drive voltage.
For preventing damage of a laser diode, it is important to avoid any excessive drive currents; even short current spikes could destroy a laser diode, e.g. in the form of catastrophic optical damage due to excessive optical intensity as the diode's output facet.Particularly if a laser diodes driver is not made for diodes with a specific maximum drive current, it should have a separate control where the maximum drive current can be adjusted, and the limit set there should be respected by any other controls, e.g. the one which is regularly used to adjust the drive current.(When the current limit is reached, the current may either be clamped to the limit value or switched off until the user reactivates the device e.g. by pushing a button.)In that way, one can greatly reduce the risk that a user accidentally draws the power knob too far; special care has to be applied only when the current limit is set.
In some cases, laser diodes are intentionally overdriven, i.e., operated with a drive current above the recommended maximum.In that way, one may achieve an increased output power, but at the cost of a reduced laser lifetime, and possibly even with the risk of instant damage.
Obviously, a laser diode driver should be relatively immune against external influences such as voltage spikes on the electrical grid or current transients resulting from faulty electrical contacts.
Different Power Levels
Laser diodes and therefore also laser diodes drivers are available in a very wide range of powers.Some low-power diodes require drive currents of only e.g. 20 mA, whereas high-power diode bars may be operated with drive currents of dozens of amperes.In case of high-power diode drivers, it is of interest to have a switching power supply and related control electronics with high power conversion efficiency – not only in order to save electricity, but also to limit the amount of waste heat which normally needs to be dissipated with additional means such as a ventilator or a water cooling system.
If the system contains multiple laser diodes, one in principle use a separate driver for each one.However, as long as independent power control of these diodes is not required, it is simpler, more convenient and more economical to operate multiple diodes with a single diode driver.Usually, the laser diodes are connected in series, since this guarantees that they are all operated with the same drive current; if they would be connected in parallel, the hottest diode may consume the largest part of the current and thus become even hotter.Also, parallel connections could lead to excessive drive currents in the electrical cables and connectors, also to a reduced efficiency of the driver, whereas higher voltages are often not a problem.For cases with a very large number of laser diodes, one may group the diodes into packages where there is a serial connection of the diodes within each package, and the different packages are driven by separate output stages of the driver (with separate current stabilization).Obviously, the via ring of the used laser diodes (e.g. common cathode or common anode) must fit to the connections of the used laser diode driver.
It is often advisable not to use a laser diode driver which is designed for a much higher drive current than required.Even if a proper current limit can be set, the accuracy of the set operation current may otherwise be worse, the current noise may be higher, and the transient protection may be not sufficiently sensitive for a low-power diode.
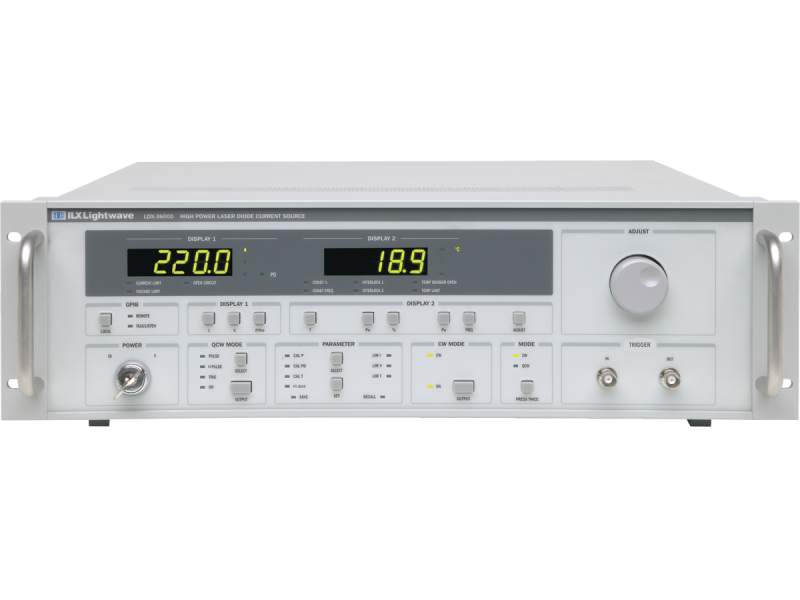
Additional Functionality
Beyond the mentioned basic functionality, laser diodes drivers can offer a number of additional functions:
Interlock Systems
Very often, a diode driver has some interlock system, which can switch off the laser in case that a certain safety condition is detected – for example, and opened device housing.It can be very useful to have multiple interlock connections for implementing advanced safety features.Some of them may treat conditions like insufficient coolant flow on a chiller in order to avoid hardware defects.
Constant Power Mode
There are devices which can stabilize the optical output power (constant power mode), based on a signal from the photodetector, which may be integrated into the laser diode package.(That is particularly often the case for fiber-coupled laser diodes.)Of course, a certain maximum drive current must never be exceeded; otherwise, a laser diode could be killed as a result of a faulty photodetector signal.Often, it is possible to switch between constant current mode and constant power mode.
Electrical Monitoring Outputs
There may be electrical outputs, e.g. delivering a voltage proportional to the laser diode current or the monitored optical power, possibly with a calibration feature.
Protective Features
The applied voltage should be monitored, and if an unusual operation voltage is detected, the device may switch off the diode in order to prevent damage.If several laser diodes are operated in series, a sudden drop of the voltage may indicate the death of one of the diodes, and it may then be wise to investigate the situation before the other laser diodes are also destroyed.Also, it is useful if the driver recognizes wrong poling of a diode, because it could be destroyed by an excessive reverse voltage.
For transient protection, the diode's cables should not simply be disconnected when switched off, but rather electrically connected together (shorted), so that electrostatic discharges cannot build up a voltage across the pins.
Temperature Control and Monitoring
Some devices have an integrated temperature controller, driving e.g. a Peltier element based on the signal of some temperature sensor.Even without a temperature stabilization feature, it can be useful to monitor the junction temperature for switching off the laser before it gets too hot.Alternatively, one may monitor the emission wavelengths, which reacts sensitively to temperature changes, unless an optical wavelength stabilization is used, e.g. based on optical feedback from a volume Bragg grating.
Also, it is sensible to monitor the internal temperature of the electronic driver device, since overheating e.g. due to a blocked air or water flow may destroy the driver and possibly the laser diode(s) in addition.
Low-noise Operation
Some drivers are made for operation with a particularly low current noise.This can be important, for example, when driving lasers for sensitive optical measurements.Low-noise operation is mostly offered for low-power devices.
Slow Start Feature and Turn-on Delay
Particularly for high-power laser diodes, it can be useful to limit the rate with which the current can be ramped up and down (slow start feature), because this reduces the internal mechanical stress related to temperature changes.In addition, a turn-on delay is often used as a safety feature; people in the room are warned about coming laser radiation before it is actually turned on.
Wavelength Tuning
Some diode lasers, in particular external-cavity diode lasers, are suitable for wavelength tuning in a substantial range.For example, a diffraction grating on a motorized stage can be used for controlling the emission wavelength.Some laser diodes drivers contain functionality for tuning the wavelength e.g. via controlling some stepper motor.
Quasi-continuous Wave Operation
Some drivers are suited for quasi-continuous-wave operation (QCW mode).This means that they can apply current pulses with an adjustable duration e.g. between 1 μs and 10 ms, which can be triggered with an external electric signals or with a built-in clock.The possible peak current may be well above the current which the driver could deliver continuously, or which the laser diode could tolerate continuously.
Short and Ultrashort Pulse Generation
They are specialized drivers for producing nanosecond or picosecond pulses, e.g. by gain switching.Here, it is particularly important to select a suitable laser diode and to properly adjust the parameters of the applied current pulses.
Current Modulation
In other cases, a laser diode driver allows some other kind of modulation of the supplied current.This can be done in many different forms.For example, a TTL input signal may be used to switch the current on or off.In other cases, an analog input signal is added to the base current set with the controls.Drivers can differ very much in terms of modulation bandwidth and depth of modulation.
Current modulation is often available only in current control mode, i.e., not in combination with output power stabilization.This is because the limited feedback bandwidth of the stabilization circle it would strongly limit the possible modulation bandwidth.
Computer Control
A diode driver may be computer-controlled, connected e.g. via a USB, GPIB or a serial interface like RS-232.It may receive inputs, e.g. concerning the requested drive current, and deliver outputs, e.g. concerning the achieved optical output power or the required diode voltage.
Different Types of Diode Drivers
Some laser diodes drivers are made as instruments specifically for use in laboratories.Here, the user usually has direct access to the device and its controls, which usually include various knobs, buttons and switches, e.g. for adjusting the diode current or temporarily switching it off.Laboratory diode drivers usually have a front panel with a digital display for the diode current, possibly also for other quantities like the applied voltage or the diode temperature, if the latter can be measured with a built-in temperature sensor.Such devices are often not built for a specific type of laser diode, but with increased flexibility for using different diodes.This implies that different maximum voltages and currents can be applied.
Some devices have a standardized housing for mounting in a rack, where they can be combined with other electronic devices.
Finally, there are driver modules for integration into other devices (e.g. mounted on a chassis heat sink) and sold as OEM packages, if not produced by the manufacturer of the system.They often have only electronic interfaces for interaction with other parts of the system electronics, and not directly with the user of the laser device.They are often used in larger quantities and available at lower prices.
Further Remarks
Laser diodes are generally not suitable for “hot plugging”: they should be connected or disconnected only while the diode driver is switched off, and proper precautions have to be taken to avoid damage by electrostatic discharge (ESD).For example, one may shorten the pins at the diode before disconnecting the wires from the driver.
Before using a diode driver within some larger system, one should check whether problems could arise due to improper grounding.Some diode drivers have one output pin connected to the case and to earth ground, and may then interfere with additional grounding on other devices.Even if the same pin is connected to earth ground at different locations, problems may result due to a “ground loop” in which magnetic fields can induce disturbing currents.
Suppliers
The RP Photonics Buyer's Guide contains 68 suppliers for laser diode drivers. Among them:
EKSMA OPTICS
EKSMA Optics offers the uniLDD universal laser diode drivers. uniLDD is a DC input power converter designed to supply CW or pulsed current for single emiter, bar or stacked laser diodes in constant current (CC) mode. Drivers can be supplied for a wide current range as well as for a wide diode compliance voltage range.
Drivers Diode Tester
TOPTICA Photonics
Apart from a well-engineered optomechanical design and the integrated laser diode, the most important part of a tunable diode laser system is its driving electronics, which is responsible for getting the most out of a laser system.
Wide mode-hop-free tuning with Littrow setups requires a well-defined interplay between piezo actuator and current driver. Drifts of the laser diode current, the temperature or the piezo voltage determine the drift of the laser frequency and the stability against mode-hopping. Noise on any of these outputs increases the laser linewidth. The digital DLC pro represents the latest stage of development of laser control electronics. Its noise and drift properties are even better than the well established and widely used preceeding electronics SYS DC 110.
Artifex Engineering
Artifex Engineering's LDD100 is a fast pulsed current source for driving laser diodes and high power LEDs. We offer this instrument with various end stages with current ranges from 1 A to 600 A. The graphical user interface is clear and intuitive to use. These drivers are ideal for testing laser diodes.
Alpes Lasers
Alpes Lasers offers QCL laser drivers for pulsed and continuous-wave operation. Pulse widths as low as 20 ns are achievable with repetition rates up to 1 MHz.
Aerodiode
Aerodiode offers a wide range of laser diode drivers as OEM devices for use by laser manufacturers or R & D teams. Some models are suitable for driving high-power diode bars or diode stacks, while others can generate nanosecond pulses for both laser diodes or SOAs. All of them have an integrated TEC controller for thermal management. Ultra-low-noise models are also available.
APIC
APIC produces a turnkey tabletop laser drive module specifically designed to operate its high power, ultra low RIN lasers. The OEM laser of choice is integrated into the laser drive module at the factory. The laser drive module includes a high-quality laser driver with a low-noise power source, current driver and accurate temperature control circuit to maintain stable laser output with minimal noise. APIC is in the process of developing a similar turnkey driver module for its Direct Modulated Lasers (DML).
A high-quality laser driver with a low-noise power source, current driver and accurate temperature controls is required. If you do not have such equipment, we recommend you consider purchasing our turnkey tabletop CW laser drive module. The drive module has power conditioning with laser and TEC control electronics designed specifically to operate our lasers with minimal noise.
Questions and Comments from Users
Here you can submit questions and comments. As far as they get accepted by the author, they will appear above this paragraph together with the author’s answer. The author will decide on acceptance based on certain criteria. Essentially, the issue must be of sufficiently broad interest.
Please do not enter personal data here; we would otherwise delete it soon. (See also our privacy declaration.) If you wish to receive personal feedback or consultancy from the author, please contact him e.g. via e-mail.
By submitting the information, you give your consent to the potential publication of your inputs on our website according to our rules. (If you later retract your consent, we will delete those inputs.) As your inputs are first reviewed by the author, they may be published with some delay.
See also: laser diodes, diode lasers, laser safety
and other articles in the categories photonic devices, lasers
Now is the Time for Training!
When your lab is closed, how to best utilize your time? With training, of course.
Some suggestions:
- Use the RP Photonics website, reading encyclopedia articles, tutorials, Photonics Spotlight articles, etc. – all for free.
- Get a tailored training course delivered through the internet – with every participant connected from home!
- Start with physical modeling in order to fully understand your systems and devices, optimize performance, create new ideas…
offers tailored training courses and powerful simulation & design software, e.g. for active and passive fiber devices, laser resonators and thin-film coatings!
The Latest Encyclopedia Articles
Here are the latest encyclopedia articles:
The encyclopedia already contains 954 articles.
See also the regularly appearing articles of the The Photonics Spotlight and the RP Photonics Software News!
In electronics, an LED circuit or LED driver is an electricalcircuit used to power a light-emitting diode (LED). The circuit must provide sufficient current to light the LED at the required brightness, but must limit the current to prevent damaging the LED. The voltage drop across an LED is approximately constant over a wide range of operating current; therefore, a small increase in applied voltage greatly increases the current. Very simple circuits are used for low-power indicator LEDs. More complex, current source circuits are required when driving high-power LEDs for illumination to achieve correct current regulation.
Basic circuit[edit]
The simplest circuit to drive an LED is through a series resistor. It is commonly used for indicators and digital displays in many consumer appliances. However, this circuit is not energy-efficient, because energy is dissipated in the resistor as heat.
An LED has a voltage drop specified at the intended operating current. Ohm's law and Kirchhoff's circuit laws are used to calculate the appropriate resistor value, by subtracting the LED voltage drop from the supply voltage and dividing by the desired operating current. With a sufficiently high supply voltage, multiple LEDs in series can be powered with one resistor.
If the supply voltage is close or equal to the LED forward voltage, then no reasonable value for the resistor can be calculated, so some other method of current limiting is used.
Power source considerations[edit]
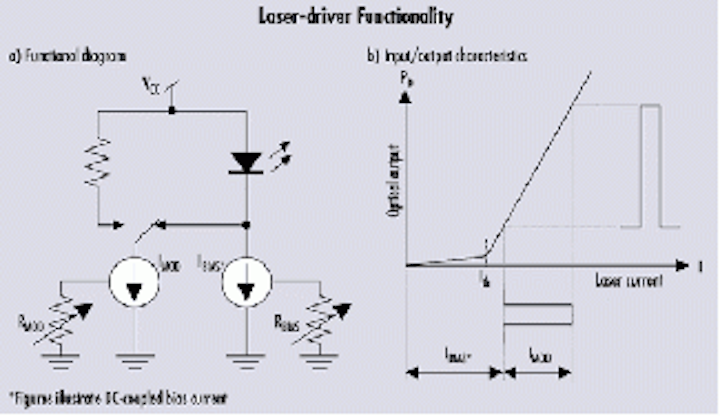
The voltage versus current characteristics of an LED are similar to any diode. Current is approximately an exponential function of voltage according to the Shockley diode equation, and a small voltage change may result in a large change in current. If the voltage is below or equal to the threshold no current flows and the result is an unlit LED. If the voltage is too high, the current will exceed the maximum rating, overheating and potentially destroying the LED.
As an LED heats up, its voltage drop decreases (band gap decrease[1]). This can encourage the current to increase.
MOSFET drivers[edit]
An active constant current regulator is commonly used for high power LEDs, stabilizing light output over a wide range of input voltages which might increase the useful life of batteries. Active constant current is typically regulated using a depletion-modeMOSFET (metal-oxide-semiconductor field-effect transistor), which is the simplest current limiter.[2]Low drop-out (LDO) constant current regulators also allow the total LED voltage to be a higher fraction of the power supply voltage.
Switched-mode power supplies are used in LED flashlights and household LED lamps. Power MOSFETs are typically used for switching LED drivers, which is an efficient solution to drive high-brightness LEDs. Powerintegrated circuit (IC) chips such as the Supertex HV9910B are widely used to drive the MOSFETs directly, without the need for additional circuitry.[2] These MOSFET-based Supertex IC chips are the most common LED drivers for solid-state lighting with LED lamps. In 2008, they were used for controlling the solid-state lighting in the Beijing National Aquatics Center during the 2008 Summer Olympics.[3]
Series resistor[edit]
Series resistors are a simple way to stabilize the LED current, but energy is wasted in the resistor.
Miniature indicator LEDs are normally driven from low voltage DC via a current-limiting resistor. Currents of 2 mA, 10 mA and 20 mA are common. Sub-mA indicators may be made by driving ultrabright LEDs at very low current. Efficiency tends to reduce at low currents,[4] but indicators running on 100 μA are still practical.
In coin cell powered keyring-type LED lights, the resistance of the cell itself is usually the only current limiting device.
LEDs with built-in series resistors are available. These may save printed circuit board space, and are especially useful when building prototypes or populating a PCB in a way other than its designers intended. However, the resistor value is set at the time of manufacture, removing one of the key methods of setting the LED's intensity.
The value for the series resistance may be obtained from Ohm's law, considering that the supply voltage is offset by the voltage drop across the diode, which varies little over the range of useful currents:
where:
- is resistance in ohms, typically rounded up to the next higher resistor value.
- is the power supply voltage in volts, e.g. 9-volt battery.
- is the LED forward voltage drop across the LED in volts, shown as on LED datasheets. Typically, the forward voltage of an LED is between 1.8 and 3.3 volts. It varies by the color of the LED. A red LED typically drops around 1.7 to 2.0 volts, but since both voltage drop and light frequency increase with band gap, a blue LED may drop around 3 to 3.3 volts.
- is the voltage drop across the switch in volts: (A) for no switch, use 0 volts, (B) for mechanical switch, use 0 volts, (C) for BJT transistor, use collector-emitter saturation voltage from the transistor datasheet.
- is the desired current of the LED in amps. The maximum current is shown on LED datasheets, for example 20 mA (0.020A) is common for many small LEDs. Many circuits operate LEDs at less than the recommended maximum current, to save power, to permit the use of a standard resistor value, or to reduce brightness.
LED arrays[edit]
Strings of multiple LEDs are normally connected in series. In one configuration, the source voltage must be greater than or equal to the sum of the individual LED voltages; typically the LED voltages add up to around two-thirds of the supply voltage. A single current-limiting resistor may be used for each string.
Parallel operation is also possible but can be more problematic. Parallel LEDs must have closely matched forward voltages (Vf) in order to have similar branch currents and, therefore, similar light output. Variations in the manufacturing process can make it difficult to obtain satisfactory operation when connecting some types of LEDs in parallel.[5]
LED display[edit]
LEDs are often arranged in ways such that each LED (or each string of LEDs) can be individually turned on and off.
Direct drive is the simplest-to-understand approach—it uses many independent single-LED (or single-string) circuits.For example, a person could design a digital clock such that when the clock displays '12:34' on a seven-segment display,the clock would turn on the appropriate segments directly and leave them on until something else needs to be displayed.
However, multiplexed display techniques are more often used than direct drive, because they have lower net hardware costs.For example, most people who design digital clocks design them such that when the clock displays '12:34' on a seven-segment display, at any one instant the clock turns on the appropriate segments of one of the digits—all the other digits are dark. The clock scans through the digits rapidly enough that it gives the illusion that it is 'constantly' displaying '12:34' for an entire minute. However, each 'on' segment is actually being rapidly pulsed on and off many times a second.
An extension of this technique is Charlieplexing where the ability of some microcontrollers to tri-state their output pins means larger numbers of LEDs can be driven, without using latches. For N pins, it is possible to drive n2-n LEDs.
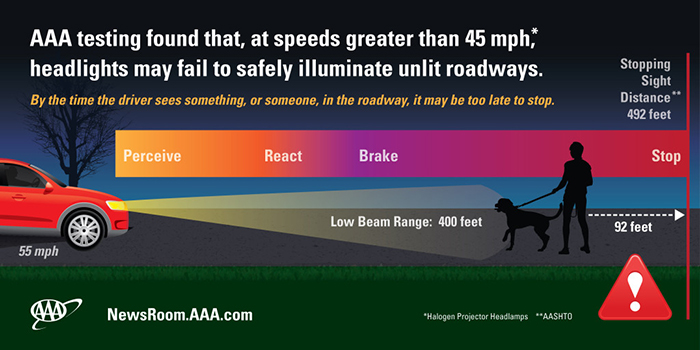
The use of integrated circuit technology to drive LEDs dates back to the late 1960s. In 1969, Hewlett-Packard introduced the HP Model 5082-7000 Numeric Indicator, an early LED display and the first LED device to use integrated circuit technology. Its development was led by Howard C. Borden, Gerald P. Pighini, and Egyptian engineer Mohamed M. Atalla, at HP Associates and HP Labs, who had engaged in research and development (R&D) on practical LEDs between 1962 and 1968.[6] It was the first intelligent LED display, making it a revolution in digital display technology, replacing the Nixie tube and becoming the basis for later LED displays.[7]
Polarity[edit]
Unlike incandescent light bulbs, which illuminate regardless of the electrical polarity, LEDs will only light with correct electrical polarity. When the voltage across the p-n junction is in the correct direction, a significant current flows and the device is said to be forward-biased. If the voltage is of the wrong polarity, the device is said to be reverse biased, very little current flows, and no light is emitted. LEDs can be operated on an alternating current voltage, but they will only light with positive voltage, causing the LED to turn on and off at the frequency of the AC supply.
Most LEDs have low reverse breakdown voltage ratings, so they will also be damaged by an applied reverse voltage above this threshold. The cause of damage is overcurrent resulting from the diode breakdown, not the voltage itself. LEDs driven directly from an AC supply of more than the reverse breakdown voltage may be protected by placing a diode (or another LED) in inverse parallel.
The manufacturer will normally advise how to determine the polarity of the LED in the product datasheet. However, there is no standardization of polarity markings for surface mount devices.[8][9]
Pulsed operation[edit]
Many systems pulse LEDs on and off, by applying power periodically or intermittently. So long as the flicker rate is greater than the human flicker fusion threshold, and the LED is stationary relative to the eye, the LED will appear to be continuously lit. Varying the on/off ratio of the pulses is known as pulse-width modulation. In some cases PWM-based drivers are more efficient than constant current or constant voltage drivers.[4][10][11]
Most LED data sheets specify a maximum DC current that is safe for continuous operation. Often they specify some higher maximum pulsed current that is safe for brief pulses, as long as the LED controller keeps the pulse short enough and then turns off the power to the LED long enough for the LED to cool off.
LED as light sensor[edit]
Drivers Diode Test
In addition to emission, an LED can be used as a photodiode in light detection. This capability may be used in a variety of applications including ambient light detection and bidirectional communications.[12][13][14]
Drivers Ideapad S100
As a photodiode, an LED is sensitive to wavelengths equal to or shorter than the predominant wavelength it emits. For example, a green LED is sensitive to blue light and to some green light, but not to yellow or red light.
This implementation of LEDs may be added to designs with only minor modifications in circuitry.[12] An LED can be multiplexed in such a circuit, such that it can be used for both light emission and sensing at different times.[12][14]
See also[edit]
- Joule thief - minimal switch-mode power supply
- Switched-mode power supply applications (SMPS) applications
- Planck–Einstein relation for the relation between band gap and photon frequency
- Shockley diode equation for the relation between forward voltage and current
References[edit]
- ^Van Zeghbroeck, Bart J. (1997). '2.2.5'. 2.2.5 Temperature dependence of the energy bandgap. Ece-www.colorado.edu. Retrieved 2009-02-15.
- ^ abWinder, Steve (2011). Power Supplies for LED Driving. Newnes. pp. 20–22, 39–41. ISBN9780080558578.
- ^'Supertex LED Drivers: The Gold Standard in Driving Solid State Lighting'. Electronic Design. Informa. 56 (25–26): 59. 2008.
Supertex's LED driver ICs were selected for controlling the solid state lighting in Beijing's 'Water Cube' Aquatic Center.
- ^ abJim Lepkowski, Mike Hoogstra, and Christopher Young. Application note AND8067/D: 'NL27WZ04 Dual Gate Inverter Oscillator Increases the Brightness of LEDs While Reducing Power Consumption'
- ^'Electrical properties of GaN LEDs & Parallel connections'(PDF). Application Note. Nichia. Archived from the original(PDF) on 2007-08-09. Retrieved 2007-08-13.
- ^Borden, Howard C.; Pighini, Gerald P. (February 1969). 'Solid-State Displays'(PDF). Hewlett-Packard Journal: 2–12.
- ^'Hewlett-Packard 5082-7000'. The Vintage Technology Association. Retrieved 15 August 2019.
- ^'Are There Standards Governing Polarity Marks?'. www.circuitinsight.com. Retrieved 19 April 2019.
- ^'How to Build a PCB: Diode Polarity (No,...'EEWeb Community. Retrieved 19 April 2019.
- ^[1]
- ^Tahan, Mohammad (Winter 2017). 'Multiple String LED Driver With Flexible and High-Performance PWM Dimming Control'. IEEE Transactions on Power Electronics. 32 (12): 9293–9306. arXiv:2002.00029. Bibcode:2017ITPE...32.9293T. doi:10.1109/TPEL.2017.2655884. S2CID43054007.
- ^ abcDietz, Paul, William Yerazunis, Darren Leigh (2003). 'Very Low-Cost Sensing and Communication Using Bidirectional LEDs'(PDF). Mitsubishi Electric Research Laboratories. Archived from the original(PDF) on 2009-02-05. Retrieved 2009-09-07.CS1 maint: multiple names: authors list (link)
- ^Bent, Sarah, Aoife Moloney and Gerald Farrell (2006). 'LEDs as both Optical Sources and Detectors in Bi-directional Plastic Optical Fibre Links'. Irish Signals and Systems Conference, 2006. IET: 345.CS1 maint: multiple names: authors list (link)
- ^ abStepniak, G.; Kowalczyk, M.; Maksymiuk, L.; Siuzdak, J. (2015-10-01). 'Transmission Beyond 100 Mbit/s Using LED Both as a Transmitter and Receiver'. IEEE Photonics Technology Letters. 27 (19): 2067–2070. Bibcode:2015IPTL...27.2067S. doi:10.1109/LPT.2015.2451006. ISSN1041-1135. S2CID23986334.
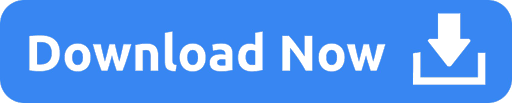